
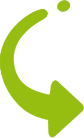
The need to deliver daily fresh products on the shelves, ever changing customer preferences, seasonal trends and compulsory legal regulations are a real challenge for any company in this sector. This industry, trading in perishable products, requires time sensitive deliveries to points of sale, while in many cases keeping the goods in fixed and mandatory temperature during transport.

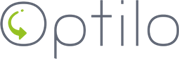
Very often, existing logistics networks hide dormant and under-utilized resources. The cost and effort to discover them is very high and the process is complicated.
Optilo enables efficient strategic analysis of warehouses, cross-docks and fleets in the distribution network. The goal is, of course, a more cost-effective distribution structure and goods flows between shipper and final consignee.
‘What if…?’ simulations, carried out with cost efficiency in mind, allow for phased implementation of improvements. This considerably reduces the risk of wrong decisions.
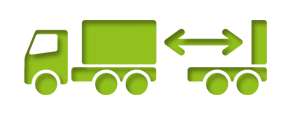
Fast and efficient scheduling of deliveries in response to changing customer demands.
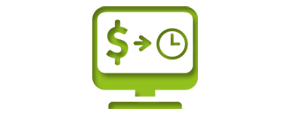
Efficient delivery schedules reduce time and distance, optimize vehicle utilization. Efficient carrier selection.

Efficient and effective management of individual process elements: from customers’ orders over scheduling deliveries to invoicing and financial analysis.
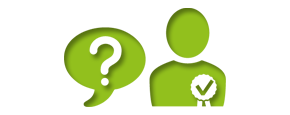
Goods delivery on the basis of a fixed schedule if required. Alerts and notifications in case of delays or deviations from the plan.

An integrated planning system that minimizes bottlenecks.

Minimizing the transport cost from the distribution center to each customer, taking into account the distances and also the frequency of the deliveries.


Auto-planning customer deliveries as well as the and inbound flows of raw materials. Selection of the most effective means of transport, execution follow-up and cost control. Key benefits include reduced transport costs, increased efficiency (automation) and customer service levels.
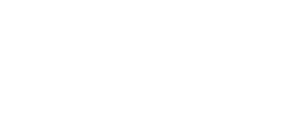
Automated communication with transport and logistics service providers, starting at the carrier selection phase until the final freight settlement, reducing e.g. the time needed for invoice checking.

Portal, allowing external parties to book time slots for loading and unloading. The benefits are mutual: the operator can fit the slots into the roundtrips and the company only has to limit itself to supervision and establishing the slot allocation rules.

Maximizes vehicle capacity utilization taking co-loading and positioning limitations into account. Reduction of wasted space.

YMS actively assists in the organization and execution of the yard management. It substantially minimizes manual activities to support these processes. Automation and standardization of yard activities by means of e.g. magnetic cards, document scans, SMS etc.
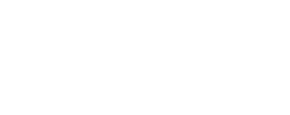
Effective communication between company, customers and drivers allows very precise job monitoring and order tracking.