
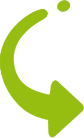
Furniture transport is one of the most challenging areas in freight forwarding. Specialist companies organize deliveries in such a way to avoid production downtimes and to deliver the finished products right on time in the stores or at the final customer. In some organizations, deliveries have to be made to private customers with limited availability for delivery (e.g. evenings or weekends). This requires excellent logistics planning and customer service management.

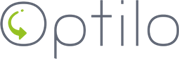
Optilo allows for efficient and flexible management of the entire process of receiving raw materials for furniture production, integration with manufacturing and warehouse systems and also for management of manufacturing process, both for stores and individual buyers. Planning, selection of means of transport and human resources, execution of orders, monitoring and control
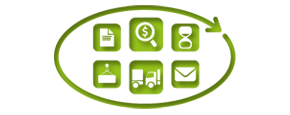
Handling the entire supply chain, from raw materials procurement through integration with manufacturing systems to organizing support for wholesale and retail market.
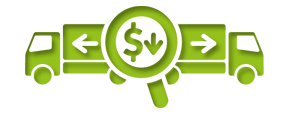
Efficient delivery schedules reduce time and distance, optimize vehicle capacity utilization. Efficient carrier selection.

Efficient and effective of individual process elements: from raw material and finished product contract matters over delivery schedules to managing loading and unloading activities.

Delivery of good can be based, if desired, on fixed schedules. Alerts in response to delays and deviations from the planning.

Automated information exchange between all parties in the supply chain: customers, product suppliers, carriers.
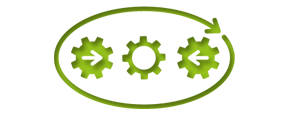
Increasing efficiency and reducing bottlenecks through integration with external clients’ and subcontractors’ systemsand telematics.

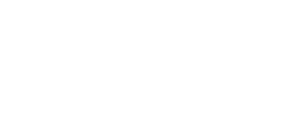
This module assists in making the right decisions within the shortest possible timeframe: automatic customer delivery scheduling, cost control and optimization of transport assets. Key benefits include lower transport costs, increased productivity, shorter execution time and improved communication with customers and drivers.
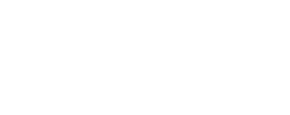
Instant information on costs related to the job execution. Cost settlement in relation to own fleet and provided carrier services. Costs are both at estimate and actual level.

Planning tasks, monitoring their lifecycle, automated execution supervision and anomaly alerts. Informing, preventing, alerting and escalating.
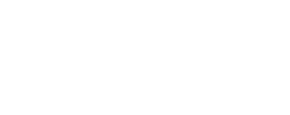
Efficient communication between operations and the driver waiting for docking using SMS or an array of lights.

YMS actively assists the organization and execution of the yard management. It substantially minimizes manual activities to support these processes. Automation and standardization of yard activities by means of e.g. magnetic cards, document scans, SMS etc.
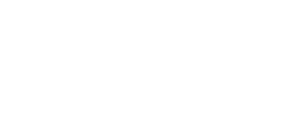
Minimizing the transport cost from the distribution center to each customer, taking into account the distances and also the frequency of the deliveries.